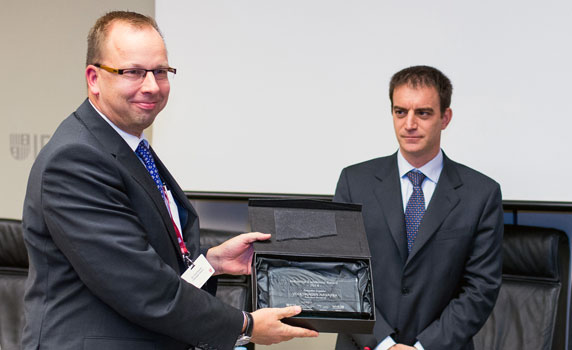
Volkswagen’s Navarra plant has won the Industrial Excellence Award 2014, beating a shortlist of top European factories, among them L’Oréal (Rambouillet, France), MDC (Kölleda, Germany) and ABB (Turgi, Switzerland).
The Pamplona plant, which manufactures the VW Polo, won praise from the jury for rapid deployment of innovative process improvements, exemplified by the use of using hawk-eye technology and breakthrough approaches such as kanbanyoke (a combination of kanban and pokayoke techniques). The jury also applauded the factory for negotiating market turbulence through internationalization (91% of the cars it manufactures are for export) and for its transparency and communication in working towards its strategic objectives.
This prestigious European prize, first awarded in 1995, is given jointly by IESE and other leading European business schools, including schools: INSEAD, WHU, RSM, Cambridge and Koç. This is the second time that the winner of the Spanish award, offered by IESE’s CELSA Chair of Competitiveness in Manufacturing, has gone on to win the European prize. John Deer Ibérica set the precedent, winning both the Spanish and European awards in 2011.
The Factory of Tomorrow
Frederic Sabrià, IESE professor and holder of the CELSA Chair of Competitiveness in Manufacturing, presided over the award ceremony at IESE in Barcelona. He also moderated a panel discussion with industry executives, entitled “The Future of Manufacturing,” during which he pointed to certain global tendencies that are shaping manufacturing systems throughout the world. These include:
shorter production cycles;
the proliferation of products;
e-commerce and online orders;
globalization and the spread of digital technology.
Sabrià also emphasized key short-term and mid-term developments such as the digitization of the supply chain and additive manufacturing.
Digitizing the Supply Chain
Interconnection and intercommunication between different teams and systems is bringing about un-stoppable changes in the flows of the supply chain. Industry leaders are already talking about Industry 4.0 and smart factories, said Prof. Sabrià.
Today’s manufacturers are beginning to combine absolute connectivity with other technological developments, such as cloud computing (which permits the centralization and storage of data in the cloud), cheap computing and big data (which make it possible to process data in bulk) and the Internet of Everything. The result is new forms of industrial organization and new manufacturing processes.
Prof. Sabrià gave the example of pronto moda (“fast fashion”) chain Shana. The company puts new designs to the test on Facebook before deciding whether to move to production. If a picture of the prototype doesn’t get a certain number of likes on social media within a few minutes, the design is scrapped.
Although there are more sophisticated and complex applications of the so-called “industrial internet,” this simple example illustrates the extent to which combining these technologies can radically transform production.
Additive Manufacturing
Additive manufacturing, or 3-D printing is set to revolutionize the production process, said Prof. Sabrià.
Víctor Paluzíe, director of Rapid Manufacturing Systems, pointed to the key benefits of this innovative technology, which is being used both for direct manufacturing and for the creation of prototypes. Advantages include shorter development times for new products, design freedom (the possibility of greater complexity without added cost), and lighter, cheaper designs (because additive manufacturing decreases the weight of components). The savings for certain components and in certain industries, said Paluzíe, are astounding. He cited the case of General Electric Aviation, which has used additive manufacturing to reduce the weight of an airplane motor by 453 kilograms and the weight of a seat belt buckle by 77%. These reductions amount to savings of several million dollars.
Íñigo Felgueroso, Managing Director of Prodintec, warned that for now, industrial 3D printing and additive manufacturing only make sense in a context of geometrical complexity, personalization and short run production. In these circumstances, and especially in the molding, aeronautics and medical sectors, 3D printing is already being used efficiently and viably. But there are still important limitations associated with the technology, he said. “Let’s remember that we can’t make a turbine for GE with a 700 euro 3D printer.”